Black powder, a mixture of nitrates with sulfur and charcoal, was originally developed during the Tang dynasty in China, in the 7th century. This was the golden age in China, known for its poetry and painting, along with gunpowder and other inventions such as wood block printing. With a population of 50 million people, and vastly expanded borders, there were many resources available for the expansion of knowledge and technology.
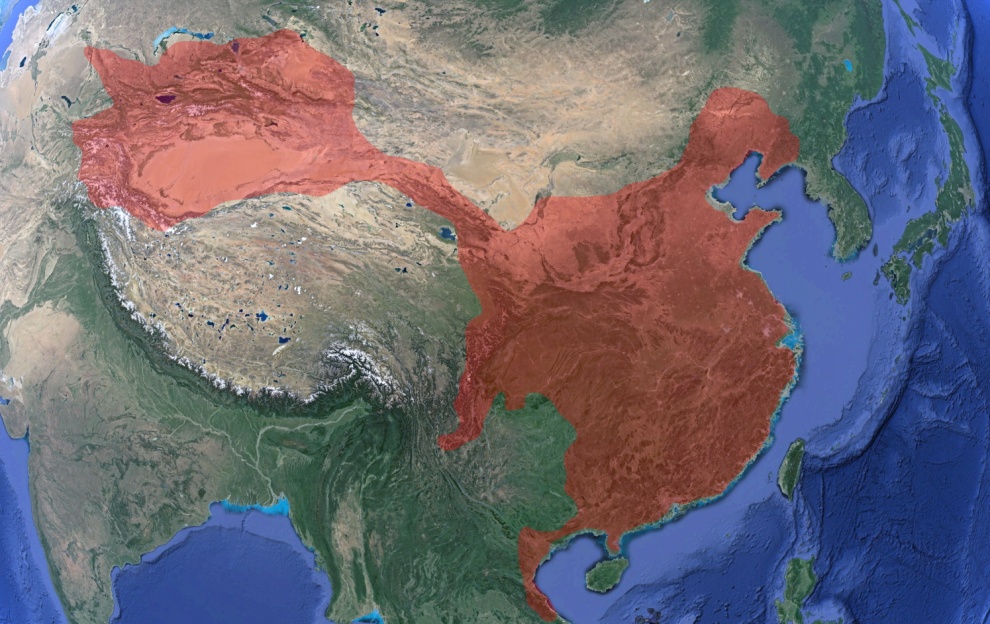
In searching for medicines, Chinese practitioners experimented with many extracts and mixtures. They were already familiar with sulfur and charcoal, both of which have medicinal uses. They were also familiar with saltpeter, which in its impure form is a mixture of several nitrates, including sodium and potassium nitrates. Purified potassium nitrate, where enough of the sodium had been removed that the resulting crystals imparted a purple color to a flame, had been available for at least three centuries prior to its use in gunpowder.
Heating and burning mixtures was a common practice in making medicines, and heating charcoal or sulfur with nitrates generates a notable reaction. The Chinese named this mixture huo yao, or "fire chemical". Early recipes for black powder, written down as early as 1044, used less nitrate than is commonly used today. The nitrate is the oxidizer, and if the mixture was to be burned in the open air, it may not have been as necessary to have a lot of oxidizer. Later uses, where the powder is confined in rockets or guns, would lead to mixtures with about 75% nitrate.
Of the three ingredients, charcoal was likely the easiest to procure. Charcoal was used in metal smelting and other industries, because it burns very hot, and the temperature can be controlled easily by controlling the flow of air. Commercial production of charcoal was an involved affair. A stack of wooden logs was carefully made and covered in sod, clay, or earth to prevent outside air from getting in, with a chimney for controlled airflow. The wood was set on fire, and once it was well started, the openings for air were closed off with more sod, clay, or earth. The whole apparatus was carefully tended for as long as 5 days or more, and any leaks that developed were covered to prevent the product from going up in smoke.
As a source of combustible carbon, charcoal has some special properties that make it work better in black powder than other sources of carbon, such as coal or graphite. It is porous, and as the mixture of materials is finely ground together, the other ingredients are packed into the pores of the charcoal, and remain finely mixed. It has other volatile compounds in it besides carbon, which reduce the ignition temperature and speed the burning. The high carbon content leads to high temperatures when burning, which is essential in making the gases expand quickly.
Sulfur is widely available in nearly pure form near volcanic regions and hot springs. As volcanic gases escape from openings in the ground, the brim of the opening becomes covered in sulfur as the gases cool (hence the name brimstone). It was used for medicines, fumigation, and bleaching. In addition to sulfur mining, the Chinese had extracted sulfur from iron pyrite as early as the 3rd century.
Sulfur ignites at a very low temperature (190° Celsius), and when finely powdered, can have a flash point as low at 166° C. Above about 444° C it becomes a gas. Along with the trace volatiles in the charcoal, sulfur speeds the burning of the final powder. The gases produced by the burning powder are carbon dioxide, carbon monoxide, and nitrogen, and at room temperature and normal atmospheric pressure, these gases would take up 380 times as much space as the original powder. But at the temperatures reached in the reaction, the gases expand to something closer to 3000 times the original volume of powder. As this happens in 25 microseconds, we hear it as a bang.
Nitrates were likely the most difficult black powder ingredient to procure. While they exist in small quantities in animal dung, extraction would have been uneconomical. However, nitrates are a byproduct of nitrifying bacteria (such as nitrobacter and nitrosomonas), which convert other nitrogen containing molecules in compost heaps into nitrates. Over time (after about two years), a dung heap becomes richer in nitrates as the bacteria grow. The result is a much better fertilizer than animal dung alone, and farmers learned to tend the manure heaps by turning them to allow the bacteria to get oxygen, to add urine to the heaps as feedstock for the bacteria, and to build the piles on beds of clay and protect them from rain and sun. With all of these careful management processes, the result was rich enough in nitrates that crystals would form on surfaces.
Potassium nitrate decomposes when heated above about 550° Celsius, releasing potassium nitrite and oxygen. In black powder at this temperature, the sulfur is already a gas, and is well above its ignition temperature (190° C). The ignition temperature of charcoal (349° C) has also been exceeded at this point. Above about 790° C, the potassium nitrite then decomposes, releasing nitrogen and more oxygen to combine with the remaining sulfur and charcoal.
Early gunpowder may have been made from those unpurified crystals of potassium nitrate, sodium nitrate, ammonium nitrate, and strontium nitrate. But potassium nitrate can be purified from those dung-heap scrapings by making use of rudimentary chemical knowledge.
First, the nitrates are leached out of the nitrified manure by pouring water into it and collecting the nitrate-laden water the next day, which is then run through more nitrified manure, to get a higher concentration of nitrates. This extra concentration saves energy, as the water will later be boiled away.
The nitrate-laden water contains calcium nitrate, magnesium nitrate, sodium chloride, and potassium chloride, as well as the desired potassium nitrate. To convert the other nitrates to potassium nitrate, potassium hydroxide is added. This is done by adding wood ashes, which are rich in potassium hydroxide. The calcium and magnesium salts precipitate out of the solution, and are filtered out.
The refining process continues by boiling the filtered liquid. Potassium nitrate is more soluble in boiling water than common salt (sodium chloride) is. The salt gradually precipitates out, where it can be removed, and organic matter floats to the top, where it can be skimmed off.
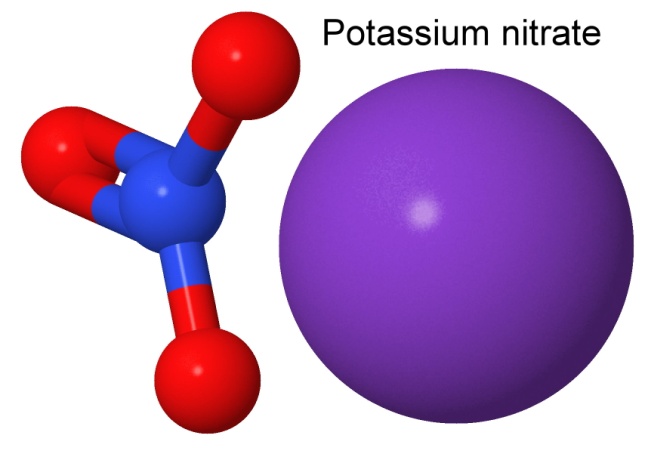
When the liquid cools, the potassium nitrate crystallizes out, and falls to the bottom, where it can be collected. The result contains 75% to 95% potassium nitrate. Further refining involves adding water to the crystals, adding protein (glue or blood) to coagulate any organic matter that can then be filtered out, and recrystallizing the potassium nitrate, stirring constantly as the mixture cools so that masses of crystals do not form (which would trap impurities between them).
Finally, the collected fine crystals are washed with a saturated solution of pure potassium nitrate (from prior refining). This cannot dissolve any more potassium nitrate, so the crystals do not dissolve, but it will wash away any remaining impurities, and dissolve any salt.
As mentioned earlier, the first Chinese black powders were likely made with impure ingredients, and without the optimum amount of nitrate oxidizer. As more experience with the manufacturing process evolved, recipes improved. One key discovery is that the burning happens faster if the mixture is very finely powdered. This is useful for making bombs and for use in small arms, but fast burning fuel is not good for large cannons or rockets. To slow down the burning, the fine powder is mixed with small amounts of water and a binding agent (such as dextrin, a modified starch), and then forced through a sieve to make larger particles with less surface area. The ingredients thus remain finely mixed, as they were in the fine powder, which guarantees proper combustion, but the lower surface area reduces the combustion speed. At the same time, the spaces between the larger grains allowed the flame to set all the grains burning at once, so the pressure buildup started sooner, and was more constant.
Burning black powder in air produces lots of nice smoke and flames, and it burns much faster than other materials do. This alone would have made it remarkable to early Chinese experimenters. But it is when black powder is confined that it produces the loud bang of the firecracker. It could be packed into bamboo tubes and thrown into a fire, creating an explosion.
The first paper firecrackers appeared around the tenth century, attributed to the Chinese inventor Li Tian. He is still celebrated in China every April 18, and parts of his workshop have been preserved by worshippers, giving us evidence for the timeline. Around the same time, the invention of the fuse allowed the user to light the firecracker and get away before it went off. Early fuses, made of straws or feather quills filled with black powder, were not very reliable. It was only much later (in the 1800's), when large amounts of black powder were used in mining, that more reliable fuses were developed.
During the Song dynasty in China (960 to 1279 AD), black powder was used in warfare as an incendiary. Since the recipes used then were low in nitrates, they burned rather than exploded. Black powder, wrapped in paper and attached to the shafts of arrows and equipped with a fuse, burned hotter than the burning pitch used earlier, and was harder to put out, since it had its own oxygen source. Hollow metal balls with holes in them were filled with black powder and lofted at enemies from catapults. Again, the very hot flames shooting out the holes ignited whatever flammable material it encountered. Sometime around 1100 the Emperor Jen stopped all export of sulfur and saltpeter, and made a state monopoly out of the manufacture of black powder, to prevent its use by enemy armies.
The Song dynasty (at least the northern part) fell to the Jin invaders from Korea when the capital Kaifeng was attacked. During that battle, in the year 1126, the first exploding bombs were used against the invaders. Because the low nitrate content of the powder could not burn fast enough to burst strong container walls, they were not much more than big firecrackers, made of bamboo or paper, producing mostly noise and smoke (although the bombs contained as much as four pounds of powder, and were probably effective incendiaries as well). But despite this new technology, the battle was lost in 1127.
By 1150, the invaders (now the Jin dynasty) were manufacturing saltpeter in manure heaps designed for that purpose, and manufacturing black powder for weapons. They perfected the recipes, adding more nitrate, until the powder could burst iron bomb casings. By holding up against more pressure, the bombs could deliver much more power than the earlier paper bombs could. When, in 1231, the invading Mongols attacked Kaifeng, these bombs were used to defend the city. The explosions charred areas scores of yards square, and could be heard over 30 miles away. The shrapnel could pierce the Mongol iron armor, and bombs lowered on chains from the city walls blew the attackers to pieces.
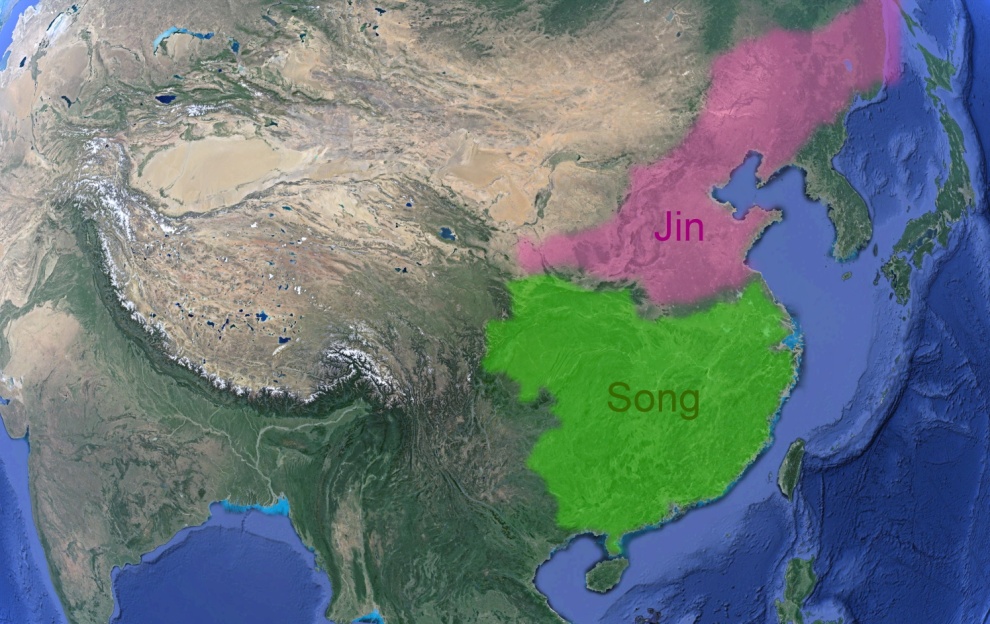
Eventually, however, the Mongols under Genghis Kahn prevailed, and the Jin dynasty fell. The Mongols with their highly effective cavalry tactics brought the new weapons to later conflicts. By 1274, under Kublai Khan, the grandson of Genghis, they attacked the remaining southern Song dynasty, adding the remainder of China to their expanding empire.
For the duration of the Mongol Empire, bomb-making technology continued to improve. Larger bombs, bombs with added shrapnel, and bombs with shrapnel mixed with noxious chemicals and waste designed to maim, blind, and infect the enemy were created and deployed. But this was also the era of the rocket.
The first rockets were likely the arrows discussed earlier, equipped with black powder in paper tubes attached to the shaft. A relatively small change to that design results in a tube that generates extra thrust for the arrow, as the powder burns, exiting through the hole made for the fuse.
Fire lances, which were hand-held tubes filled with black powder and ignited, had been used for some time already as front-line weapons, spewing fire for several feet in front of the operator. We can think of these as an early flame-thrower. The flames would persist on the order of five minutes or so. An operator of such a weapon might feel a force pushing him back, but it would not be much unless there was some constriction (a nozzle) where the flames left the tube. This would allow pressure to build up in the tube, propelling the gases forward at a higher speed. Fire lances were used by the Jin defending Kaifeng from the Mongols in 1232, and may have been in use as early as 1000.
As early as 1256, when the Mongols attacked the Assassins, the use of rocket assisted arbalest arrows allowed ranges of up to two miles. A type of large crossbow, the arbalest likely provided much of the propulsive power, but to reach that distance, the rocket would have certainly helped. With a delayed fuse, a rocket could take over the propulsion before the arrow pointed down, adding to the range, and possibly to the penetrating power on impact. It would not have had to be powerful enough to launch itself.
When a rocket is self-launched, its initial velocity is low, and this greatly reduces the accuracy. Starting with an arrow launched from a powerful arbalest, the rocket would ignite when the aerodynamics of the speeding arrow had already stabilized it, making it an effective weapon. And there would obviously be less powder needed in the rocket. Without the rocket assist, arbalests of the time had a range of about a quarter mile of a mile.
Unassisted by the speed and aerodynamics of an arrow, a tube filled with powder and closed at one end would propel itself along the ground in a random fashion, unable to aim. Such devices were in use some time after 1224, and were known as "ground rats", and provided amusement in the court of the Emperor.
One record of rockets being used as signaling devices dates to 1272, during the Mongol siege of Xiangyang. Defenders had quietly left the city in boats in the night, to try to bring in supplies. Seeing masts in the dark, they signaled what they thought were Song ships come to help. The ships were instead manned by Mongols, who saw the flares and captured the boats and crews, leaving the city cut off from supplies. These signal rockets may have been the first rockets that did not need the assistance of a launching bow, as accuracy would not be as important for this use.
Rockets continued to improve in subsequent years. Technicians learned to increase the surface area of the burning front by making the powder charge hollow. The powder thus formed its own tube inside the containing tube. Nozzles were made to increase the pressure, so the gases would escape at higher speed. This greatly increased the propulsive force. As with the arrows before them, rockets could carry explosive charges. Adding a second stage, so that one rocket lifted another one, gave them still greater range.
Not much has survived regarding the methods by which the early makers of black powder practiced their craft. But we do have more recent documents, such as one from the American Civil War, where the practice of making saltpeter (potassium nitrate) for the Confederate war effort was laid out in a pamphlet encouraging farmers to produce it.
The northern blockade was quite effective in cutting off supplies to the Confederacy. As early as 1862, barely a year into the four-year war, it was recognized that supplies of critical war materials, such as saltpeter, might run out if hostilities continued longer than Confederate planners had expected. Since the production of saltpeter takes 18 to 24 months, getting farmers to begin production was prudent.
The task fell to Joseph LeConte, a professor of chemistry and geology in South Carolina. In fourteen pages, he discusses the current state of the art in making saltpeter.
He begins:
By the request of the Chief of the Department of the Military, under authority of the Executive Council, I have been induced to publish, for the instruction of planters and manufacturers, a very succinct account of the most approved methods of manufacturing saltpetre. In doing so, I shall aim only at brevity and clearness.
The general conditions necessary to the formation of saltpetre are: 1st, the presence of decaying organic matter, animal or vegetable, especially the former; 2d, an alkaline or earthy base, as potash or lime; 3d, sufficient moisture; 4th, free exposure to the oxygen of the air; and 5th, shelter from sun and rain.
...By these means, if diligently used in all parts of the State, it is hoped that an immediate and not inconsiderable amount of saltpetre may be obtained. It is not believed, however, that the supply thus obtained will be sufficient for the exigencies of the war. It is very important, therefore, that steps should be taken to insure a sufficient and permanent supply of this invaluable article. This can only be done by means of nitre-beds. I proceed, then, to give a very brief account of the method of making these.
The most important prerequisite in the construction of nitre-beds in such manner as to yield nitre in the shortest possible time, is a good supply of thoroughly rotted manure of the richest kind, in the condition usually called mould, or black earth. It is believed that in every vicinity a considerable supply of such manure may be found, either ready prepared by nature, or by the farmer and gardener for agricultural and horticultural purposes.
To make the bed, a floor is prepared of clay, well rammed, so as to be impervious to water. An intimate mixture is then made of rotted manure, old mortar coarsely ground, or wood ashes (leached ashes will do), together with leaves, straw, small twigs, branches, &c. to give porosity to the mass, and a considerable quantity of common earth, if this has not been sufficiently added in the original manure-heap. The mixture is thrown somewhat lightly on the clay floor, so as to form a porous heap four or five feet high, six or seven wide, and fifteen feet long. The whole is then covered by a rough shed to protect from weather, and perhaps protected on the sides in some degree from winds.
The heap is watered every week with the richest kinds of liquid manure, such as urine, dung-water, water of privies, cess-pools, drains, &c. The quantity of liquid should be such as to keep the heap always moist, but not wet. Drains, also, should be so constructed as to conduct any superfluous liquid to a tank, where it is preserved and used in watering the heaps.
The materials are turned over to a depth of five or six inches every week, and the whole heap turned over every month. This is not always done, but it hastens very much the process of nitrification. During the last few months of the process, no more urine, nor liquid manure of any kind, must be used, but the heaps must be kept moist by water only. The reason of this is, that undecomposed organic matter interferes with the separation of the nitre from the ley. As the heap ripens, the nitre is brought to the surface by evaporation, and appears as a whitish efflorescence, detectible by the taste.
I imagine it was not that common for farmers to routinely check the taste of their manure heaps, but LeConte seems unconcerned with this issue.
When this efflorescence appears, the surface of the heap is removed, to the depth of two or three inches, and put aside under shelter, and kept moist with water. The nitre contained is thus considerably increased. When the whitish crust again appears, it is again removed until a quantity sufficient for leaching is obtained. The small mound which is thus left is usually used as the nucleus of a new heap. By this method it is believed that an abundant supply of nitrified earth, in a condition fit for leaching, may be obtained by autumn or early winter.
LeConte describes four methods of preparing the nitre beds. The first is the French method, where the compost is mixed with mortar and ashes in layers, so the alkali in the mortar and ash can work on the nitrates as the bacteria are producing it (of course he knows nothing about bacteria at this time).
The second method is the Prussian method:
Five parts of black earth and one of spent ashes or broken mortar are mixed with barley straw, to make the mass porous. The mixture is then made into heaps six feet high and fifteen feet long with one side perpendicular (and hence called walls), and the opposite side sloping regularly by a series of terraces or steps.
Straight sticks are generally introduced, and withdrawn when the mass is sufficiently firm. By this means air and water are introduced into the interior of the mass. The heap is lightly thatched with straw, to protect from sun and rain. The whole is frequently watered with urine and dung-water.
The perpendicular side being turned in the direction of the prevailing winds, the evaporation is most rapid on that side. The liquid with which the heap is watered is drawn by capillarity and evaporation to this side, carrying the nitre with it, and the latter effloresces there as a whitish crust. The perpendicular wall is shaved off two or three inches deep as often as the whitish incrustation appears, and the material thus removed is kept for leaching.
The leached earth, mixed with a little fresh mould, is thrown back on the sloping side of the heap, and distributed so as to retain the original form of the heap. Thus the heaps slowly change their position, but retain their forms. This method yields results in about a year-- probably in our climate in eight months.
The Swedish method is simpler, just mixing everything in a heap, and turning it:
Every Swede pays a portion of his tax in nitre. This salt is therefore prepared by almost every one on a small scale. The Swedish method does not differ in any essential respect from those I have already described.
First a clay floor; upon this is placed a mixture of earth, mould, spent ashes, animal and vegetable refuse of all kinds. Small twig branches, straw and leaves are added, to make the mass porous; a light covering, to protect from weather, frequent watering with urine or dung-water, and turning over every week or two.
The process is precisely the same as the French, except that the process of preparation and nitrification are not separated. I only mention it to show that nitre may be made by every one on a small scale. By this method the beds are ripe in two years-- perhaps in less time in this country.
The last method is the Swiss method, where a stable is built on a hill, and collecting the animal droppings in a pit:
The method practiced by the small farmers in Switzerland is very simple, requires little or no care, and is admirably adapted to the hilly portions of our State.
A stable with a board floor is built on the slope of a hill (a northern slope is best), with one end resting on the ground, while the other is elevated, several feet, thus allowing the air to circulate freely below.
Beneath the stable a pit, two or three feet deep, and conforming to the slope of the hill, is dug and filled with porous sand, mixed with ashes or old mortar.
The urine of the animals is absorbed by the porous sand, becomes nitrified, and is fit for leaching in about two years. The exhausted earth is returned to the pit, to undergo the same process again.
This leached earth induces nitrification much more rapidly than fresh earth; so that after the first crop the earth may be leached regularly every year.
A moderate-sized stable yields with every leaching about one thousand pounds of saltpetre.
Once the nitre beds have produced the nitrates, they must be extracted from the mess:
When the process of nitrification is complete, the earth of the heaps must be leached. Manufacturers are accustomed to judge roughly of the amount of nitre in any earth by the taste. A more accurate method is by leaching a small quantity of the earth, and boiling to dryness, and weighing the salt.
There is much diversity of opinion as to the percentage of nitre necessary to render its extraction profitable. The best writers on this subject vary in their estimates from fifteen pounds to sixty pounds of salt per cubic yard of nitrified earth. The high price of nitre with us at present would make a smaller percentage profitable. This point, however, will soon be determined by the enterprising manufacturer.
In the process of leaching, in order to save fuel, we must strive to get as strong a solution as possible, and at the same time to extract all or nearly all the nitre. These two objects can only be attained by repeated leachings of the same earth, the ley thus obtained being used on fresh earth until the strength of the ley is sufficient.
A quantity of nitrified earth is thrown into a vat, or ash-tub, or barrel, or hogshead with an aperture below, closely stopped and covered lightly with straw. Water is added, about half as much in volume as the earth. After stirring, this is allowed to remain twelve hours. Upon opening the bung, about half the water runs through containing, of course, one-half the nitre. Pure water, in quantity half as much as first used, is again poured on, and after a few moments run through. This will contain one-half the remaining nitre, and therefore one-fourth of the original quantity. Thus the leys of successive leachings become weaker and weaker, until, after the sixth leaching, the earth is considered as sufficiently exhausted. The exhausted earth is thrown back on the nitre-beds, or else mixed with black earth to form new beds. The leys thus obtained are used upon fresh earth until the solution is of sufficient density to bear an egg. It then contains about a pound of salt to a gallon of liquid.
The clever way of determining the specific gravity (density) of the solution on a farm without special equipment is notable: just see if the solution will float an egg.
The next step is to convert all the nitrates into potassium nitrate. Nitrates of lime and magnesia refer to calcium and magnesium nitrates. The calcium and magnesium take up the carbonate and hydroxide from the ashes, and precipitate out:
The ley thus obtained contains, besides nitrate of potash (nitre), also nitrate of lime and magnesia, and chlorides of sodium and potassium. The object of the next process is to convert all other nitrates into nitrate of potash. This is done by adding wood ashes. The potash of the ashes takes all the nitric acid of the other nitrates forming the nitrate of potash (nitre), and the lime and magnesia are precipitated as an insoluble sediment. Sometimes the ashes is mixed with the nitrified earth and leached together, sometimes the saltpetre ley is filtered through wood ashes, sometimes the ley of ashes is added to the saltpetre ley. In either case the result is precisely the same.
The ley thus converted is then poured off from the precipitate, into copper or iron boilers. It still contains common salt (chloride of sodium) in considerable, and some other impurities in smaller, quantities. It is a peculiarity of nitre, that it is much more soluble than common salt in boiling water, but much less soluble in cold water. As the boiling proceeds, therefore, and the solution becomes more concentrated, the common salt is, most of it, precipitated in small crystals, as a sandy sediment, and may be raked out.
Much organic matter rises as scum, and must also be removed. When the concentration has reached almost the point of saturation, the boiler must be allowed to cool. This is known by letting fall a drop of the boiling liquid upon a cold metallic surface; if it quickly crystallizes, it is time to stop the boiling.
It is now poured into large receivers and left to cool. As the ley cools, nearly the whole of the nitre separates in the form of crystals, which sink to the bottom. These are then removed, drained by throwing them in baskets, and dried by gentle beat. The mother-liquor is either thrown back into the boilers, or else used in watering the heaps.
The product thus obtained is the crude saltpetre of commerce. It still contains fifteen to twenty-five per cent. of impurities, principally common salt (chloride of sodium), chloride of potassium and organic matter. In this impure form it is usually brought to market.
LeConte could have stopped there, as his job is done — he has instructed farmer in how to bring potassium nitrate crystals to market, where refiners can process them into a form pure enough for gunpowder. Instead, he continues, describing the final refining process:
One hundred gallons of water is poured into a boiler, and crude saltpetre added from time to time, while the liquid is heating, until four thousand pounds are introduced. This will make a saturated solution of nitre.
The scum brought up by boiling must be removed, and the undissolved common salt scraped out. About sixty gallons cold water is now added gradually, so as not to cool the liquid too suddenly. From one to one and a-half pounds of glue, dissolved in hot water, is added, with stirring. Blood is sometimes used instead of glue. The glue seizes upon the organic matter, and they rise together as scum, which is removed.
Continue the boiling until the liquid is clear. The liquid is then suffered to cool to one hundred and ninety-four degrees, and then carefully ladled out into the crystallizers. These are large shallow vats, with the bottom sloping gently to the middle. In these the cooling is completed, with constant stirring. In the process of cooling nearly the whole of the nitre is deposited in very fine, needle-like crystals, which, as they deposit, are removed and drained.
In this condition it is called saltpetre flour. The object of the constant stirring is to prevent the aggregation of the crystals into masses, from which it is difficult to remove the adhering mother-liquor.
The saltpetre flour is then washed of all adhering mother-liquor. For this purpose it is thrown into a box with a double bottom; the lower bottom with an aperture closely plugged, and the false bottom finely perforated. By means of a watering pot a saturated solution of pure nitre is added, in quantity sufficient to moisten thoroughly the whole mass.
After remaining two or three hours to drain, the plug is removed and the solution run out. This is sometimes repeated several times. The saturated solution of nitre cannot, of course, dissolve any more nitre, but dissolves freely the impurities present in the adhering mother-liquor.
Last of all, a small quantity of pure water — only about one pound to fifty-three pounds of the nitre to be washed — is added in the same manner, and run off at the end of two hours.
The nitre is now dried by gentle heat and constant stirring, and may be considered quite pure, and fit for the manufacture of gunpowder.
After a section on how to analyze the resulting crystals for purity, LeConte concludes with some words for those who might think this is all too much trouble:
In conclusion, a word by way of encouragement to manufacturers in undertaking this work.
It will be seen that under the most favorable circumstances saltpetre cannot be made in any considerable quantity in less than six or eight months, and that if we commence now the preliminary process of preparing black earth, so as to insure a sufficient and permanent supply, results cannot be expected under eighteen months or two years.
Let no one be discouraged by this fact, under the idea that the war may not last so long, and all their work may be thrown away. There is every prospect now of the war continuing at least several years, and of our being thrown entirely on our own resources for war materials. Besides, even if the war should be discontinued, the work is by no means lost.
The method of preparing and making saltpetre-beds is precisely the most approved method of making the best manure, and all the labor and pains necessary for the preparation of black earth, and the construction of saltpetre-beds, and which I hope to induce my fellow-countrymen to undertake under the noble impulse of patriotism, ought to be annually undertaken by every planter, under the lower impulse of a wise self-interest, and would be amply rewarded in the increased production of field crops.
And what became of Joseph LeConte? He was thoroughly disgusted by the loss of the war, and by Reconstruction, claiming that the "sudden enfranchisement of the negro without qualification was the greatest political crime ever perpetrated by any people". Apparently, the irony of this statement in the face of slavery was lost on him. He fled the conditions he so deplored, and moved to Berkeley, California, to become a professor of geology there. He became friends with John Muir in Yosemite Valley, and co-founded the Sierra Club.